
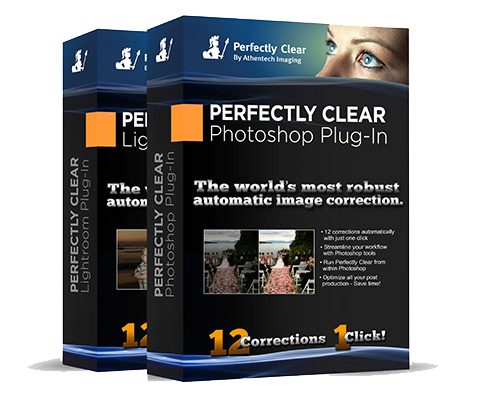
This is due to the heat generated by the concentration of material in the cup versus heat that is dissipated from the sheet casting. For example, a 200 gram mass of Crystal Clear™ 200 will cure faster if left to cure in a conical vessel (cup) versus a casting dispersed as a thin sheet measuring 3 centimeters square by 1 mm thick. in finished casting.Ĭasting Thickness & Cure Time - The cure time and ultimate shrinkage of all Crystal Clear™ products will vary depending on mass concentration, thickness of the casting, mold configuration, etc.
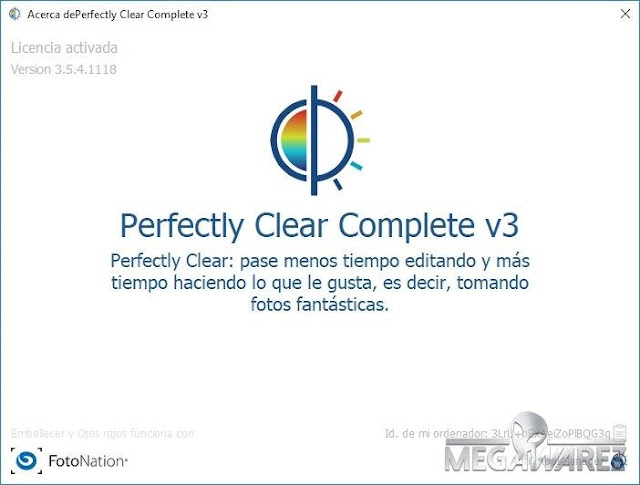
This will minimize chances of fish-eyeing, suck back, corner rounding, large bubbles, etc. If you are unsure about surface compatibility, a small scale trial casting should be made.įor Best Results Before Pouring Crystal Clear™ Into Mold: Pre-heat rubber mold at 212☏ / 100☌ for 4 hours. If using Mold Max™ silicone to prevent cure inhibition, post-cure newly cured silicone mold for 8 hours at 150° F / 60° C and let cool prior to casting resin. Selecting A Mold Rubber - Pour into a urethane rubber mold ( Vytaflex™ urethane – release agent required), tin cured silicone mold ( Mold Max™ silicone) or Mold Star™ 15, 16 or 30 platinum cured silicone ( not Mold Star™ T Series). Mixing sticks should be flat and stiff with defined edges for scraping the sides and bottom of your mixing container. Mixing containers should have straight sides and a flat bottom. Use in a low humidity environment (below 50% RH). Wearing a NIOSH approved respirator will minimize inhalation of residual fumes. Wear safety glasses, long sleeves and rubber gloves to minimize contamination risk. Environmental humidity should be as low as possible. These products have a limited shelf life and should be used as soon as possible. Safety - Store and use at room temperature (73☏/23☌).
